The Age of the Internet of Things is in full swing—and manufacturing will never be the same.
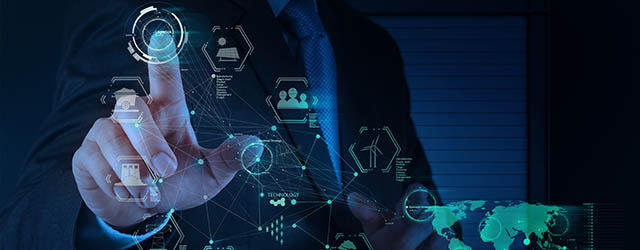
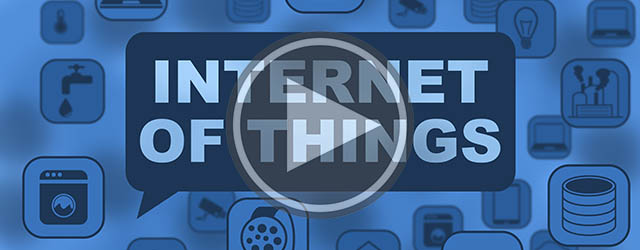
Call it the next big thing. Really big. Over the past 20 years or so, the Internet has forever altered how things get made. Whether it’s computer-assisted design, or Web-based inventory management, or digital diagnostics, the Internet has forged a more streamlined—and thus more profitable—way of manufacturing goods.
The revolution is far from over. The advent of embedded technology in individual components of manufactured goods and other devices—along with wider networking—holds the promise of exponential advances for both the supply chain and the factory line. With the Internet of Things, products will be inextricably linked to the information about them, providing a huge boost to lean manufacturing and the cash-conversion cycle. The stakes are immense. This latest evolution is predicted to boost the revenues of global manufacturing by $15 trillion over the next 15 years. Companies that don’t fully embrace IoT risk falling behind competitors—or worse.
On March 26, Global Finance, in partnership with the Government of Ontario, hosted a panel discussion on the future of manufacturing. The august group of experts included Stephan Biller, chief manufacturing scientist at General Electric; Rick Huijbregts, vice president for industry transformation at Cisco Canada; Brad Jackson, vice president for strategic business development at Celestica; Walid Negm, global research and development director for Accenture Technology; and Steve West, senior director for business development at QNX Software Systems (a unit of Blackberry Technology Solutions).
The panel, which—appropriately—was a webinar, was led by Global Finance executive editor, Denise Bedell.
At its core, IoT is a fairly simple concept. As Bedell pointed out, “The IoT is about networking objects to gather and act on data about those objects and their interaction with the world around them.”
One example: With software embedded in machines on the factory floor, manufacturers can access and monitor real-time data about production, thus boosting efficiency. And since the software is connected to the Internet, employees in remote locations can see data about output and tweak supply lines to better sync the flow of parts headed for final assembly.
This basic concept, however, could turn manufacturing on its head. And the impact won’t be limited in scope. “The IoT has the potential to positively disrupt virtually every industry vertical that is out there,” said QNX’s West. That list runs the gamut from aerospace to healthcare to energy. Any device, any product with embedded software can be networked and transmitted over the Net.
Bear in mind, this is not a technology of the future, not the stuff of science fiction. It’s already here. The “IoT cat is out of the bag,” said Accenture Technology’s Negm. Deployment of initial applications won’t take long. As General Electric’s Biller noted, “enterprises can instantly begin employing IoT technology to connect the myriad data they already collect but that don’t necessarily talk to each other yet at a system level.”
This aggregation of information about parts and products and machinery—such as whether they’re functioning properly—will generate immediate returns. Experts say the IoT can quickly help businesses contain—or reduce—production costs. “Maintenance friendliness is a key driver for asset owners or operators,” said Accenture’s Negm. “If you manage a plant and want to make it more efficient, start by getting the low-hanging fruit.”
Longer term, scientists and corporate technology executives see the Internet of Things as Industrial Revolution 4.0. The possibilities of such technology test the limits of the imagination. Cisco Canada’s Huijbregts offered an example. “What if manufacturing is disrupted in such a way where all I have to do to get a product is download a file for some new design from the Internet and then 3D print it in my living room? “
Already, 3D printers are producing, among scores of things, computers and laptops and medical implants and devices. Car parts, too, have been manufactured using 3D printing.
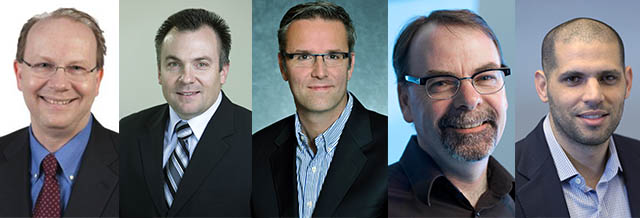
READJUSTMENT REQUIRED
Indeed, West used the automotive industry as an example. With the IoT, companies can collect real-time data during the testing of a new model. That nifty trick is accomplished by networking black boxes installed on test fleets and containing the devices engineers use to analyze performance data. The information can indicate problems before the cars even get off the test track. “There is a new demographics and consumer space out there that has been brought up with very rapid innovation cycles,” said West. “For the automotive industry, it is absolutely critical to bring new products to market quickly.”
For corporate executives, it is crucial to move swiftly in adopting the technology. That means they will have to readjust their ways of thinking. But for managers at companies already generating substantial profits, altering a winning formula can be extremely threatening. Ignoring a breakthrough in the making of things, however, could prove to be disastrous. “The model of innovation that underpins our system today is really changing,” said Jackson of Celestica. “We now see a more collaborative, externally oriented sourcing of innovation.”
Managers at both large and small companies must embrace this new ecosystem of open, crowd-sourced innovation. And CFOs and treasurers can help push top-level buy-in by using traditional yardsticks. “The number-one thing firms need to understand is the efficiency ROI [return on investment] of an IoT investment to help build a case for that investment,” said West. “The introduction of IoT technology doesn’t come for free.”
Most times, it won’t be hard to make the case. Biller noted that General Electric recently set up a competition for the redesign of a nonstrategic component of a jet engine. The challenge was issued globally. No one was excluded. “We thought we would get 30, maybe 40 entries but we received close to 700,” he recalled. “And the winning design, from Indonesia, managed to reduce the part’s weight by 75%.”
Beyond ROI, backers of this new technology will have to convince management that the IoT is secure. Certainly, embedding networking software in individual components moving along the supply-chain offers cybercriminals more avenues for entry. “There are only two kinds of companies,” Huijbregts noted. “Those that have been hacked and those that don’t know they have been hacked.”
Although investments in security are not sexy, the expert panel agreed that they are more vital than ever. “The solution lies in raising awareness at the executive level and getting to a good understanding of industrial control system security,” said Negm of Accenture. “Firms must prioritize innovative ways of getting ahead of the threat.”
And ahead of rivals. In the world of fast-evolving technology, competition could come from unexpected quarters. As Huijbregts warned, enterprises must “realize that if they don’t change, some start-up led by a bunch of teenagers will come up with something we didn’t even see coming.”