The pandemic laid bare weaknesses of dispersed lines and just-in-time delivery. Technology offers new tools for management as companies shift production post-pandemic.
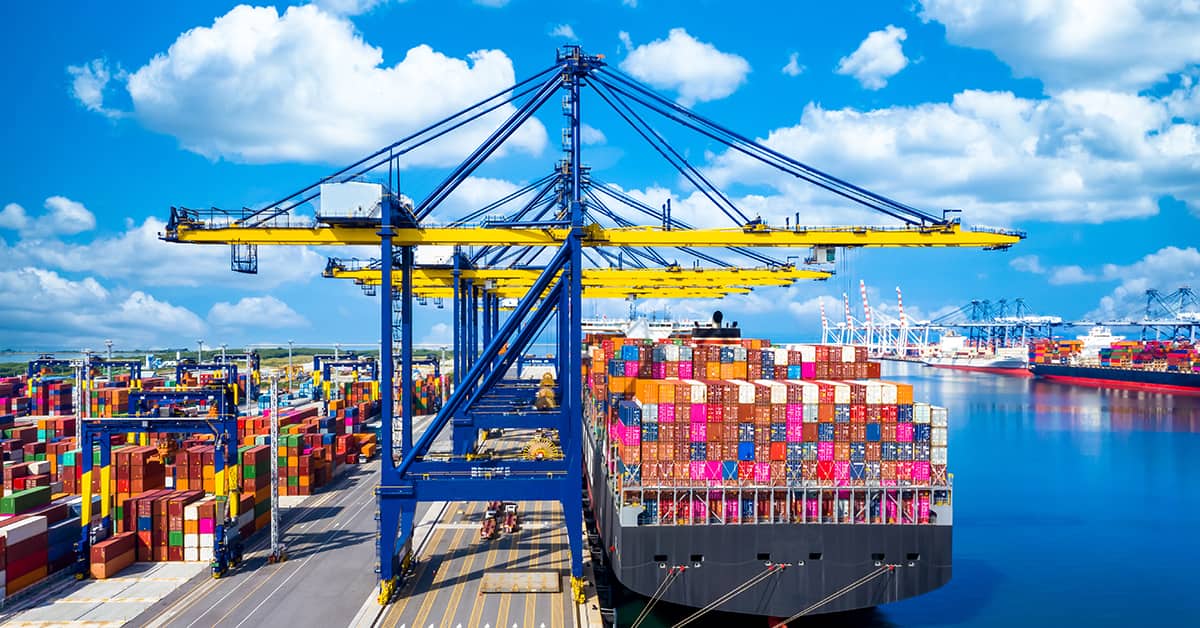
Speak to anyone who works in supply chain management these days, and they’re likely to tell you we’re living through one of the most transformational and disruptive periods in the business.
Leaner manufacturing models, in which companies hold minimal inventory and safety stock to streamline costs, weren’t prepared for the sudden spikes in demand caused by the Covid-19 pandemic. The crisis brought to light risks and dependencies inherent in pre-pandemic supply chain systems.
Take the current global semiconductor chip shortage. It may be due to a pandemic-driven production delay; but Evan Quasney, vice president of global supply chain solutions at planning-software company Anaplan, notes that having more than 50% of that production capacity concentrated in a single location (Taiwan) was poor risk management by the industry—now laid bare by the pandemic.
Suffice to say, the events of the last 18 months are likely to unleash widespread changes in global supply chains for many years to come.
Beyond Just-In-Time
Shanella Rajanayagam, a trade economist at HSBC Bank, says some businesses are now moving to hold higher volumes of components than required under just-in-time manufacturing, in order to mitigate future trade disruption. Taiwan Semiconductor Manufacturing Company—the world’s largest semiconductor manufacturer—expects customers to gradually accumulate higher levels of inventory through this year. Carmaker Toyota Motor has been stockpiling key components for the past four months, for example, notes Rajanayagam in a recent report.
But stockpiling inventory doesn’t work in every industry. Thomas Maurisset, vice president of supply chain at Valrhona, says the French chocolatier will need to support a diversity of operating models moving forward. “Just-in-time is one solution when we’re facing volatile demand and it’s difficult to build safety stock,” he explains. “But the shelf life of our product is very short, so there’s a limit to how much stock we can build.”
One of the overarching themes as companies reconfigure their supply chains is building in greater resiliency against future shocks. “Covid-19 wasn’t just a blip,” says Quasney. “Supply chain disruptions are part of the new normal.” He argues that the pandemic highlights the need for the operations side of the business to have more voice at the boardroom table. “We can expect to see a shift from the supply chain as a cost center to one that delivers a competitive advantage,” he says. “Companies that recognize the importance of operations and have a strong supply chain function are able to continuously deliver goods to market.”
Digital technologies will be a critical component of every company’s supply chain moving forward. They help optimize operations and achieve cost-saving goals, while enabling better customer-responsiveness from suppliers all along the chain.
Executives in this space talk a lot about the “supply chain control tower”—a dashboard of data, key performance indicators and other metrics that help managers achieve real-time, end-to-end visibility of their supply chains. Advances in artificial intelligence (AI) and machine learning, and new technologies such as the Internet of Things (IoT) and 5G, will make that control tower a lot smarter.
Smart sensors or devices connected to the internet will enable information to be captured at different stages of the production and logistics process, making it easier to track the status and location of goods as they physically move through the supply chain. “The IoT is really taking off in the supply chain,” says Quasney. “However, questions exist around security.”
Additionally, a control tower is only as good as its user. According to a report by research and advisory firm Gartner, in the next two to three years, supply chains will see a lot of investment in AI and advanced analytics, and real-time data But Gartner expects that even looking ahead to 2023, “less than 5% of control-tower-like deployments will fulfill their end-to-end potential due to mindset and cultural obstacles.”
Maurisset says automated planning and analytics tools have given Valrhona better visibility on most stages of production—from where the cocoa it uses is sourced right down to the finished product. “The missing part is the last mile: the delivery part,” he says. “Not everyone is connected to the same solution. They need to be convinced to go in that direction.”
Abe Eshkenazi, CEO of the Association for Supply Chain Management, says there is no shortage of funds for technology investment in supply chains, but they need to be matched with investment in workforce development. “It’s hard to fill most of the job openings in supply chain because of a lack of qualified candidates,” he says.
More Sustainable Suppliers
More than 30% of companies reported ramping up environmental, social, and governance (ESG) due diligence on suppliers during the pandemic, according to credit insurance company Euler Hermes’ December 2020 survey of more than 1,000 companies across the US, the UK, France, Germany and Italy. This rate was even higher (39%) among more-digitalized companies. Eshkenazi says visibility of your supply chain and sustainability go hand in hand. “You need transparency into the lower tiers—tier 2 and tier 2 suppliers,” he explains. But he says half of companies still lack that visibility.
In the past, sustainability was backward looking, says Anaplan’s Quasney. “Now companies want to know what your ESG plan is for the next five years.” Building more-sustainable chains is also forcing companies to think about moving distribution and manufacturing closer to the customer. “From France, we can deliver directly to our customers in Europe,” says Maurisset. “But internationally, we’re using sea freight and trains to transport our product to China and Asia. This has its limitations. Do we start building regional hubs in the Americas and Asia or pilot manufacturing sites in other cities? How far do we want to go to protect the planet and people?”
Post-pandemic companies are also searching for alternative supply solutions to activate when needed. Some companies are contemplating nearshoring (bringing production to a nearby country) or reshoring (bringing production back home) to try and minimize the impact disruptions can have on global supply chains. However, Euler Hermes’ survey finds that less than 15% of companies are considering reshoring and estimates around 30% are considering nearshoring. “Multishoring or diversification is also on the agenda,” it says, as companies look for cost-effective supply and production solutions.
“China still features relatively prominently for companies looking for new locations for production,” says Françoise Huang, senior economist for Asia Pacific at Euler Hermes. “It’s not the end of globalization. When looking at China, you still have 30% of UK companies mentioning China in their top three locations for new suppliers. It’s lower in the US; but China will still feature prominently in global supply chains, as reshoring means increased labor costs.”
Nearshoring may not make sense from a short-term cost perspective, but it could help companies achieve their sustainability objectives and reduce energy consumption, says Quasney. “We may see governments provide incentives for companies to nearshore. Industrial policy will become more important.”