The diversification of the world’s supply chains is leading to a new look compared to the past.
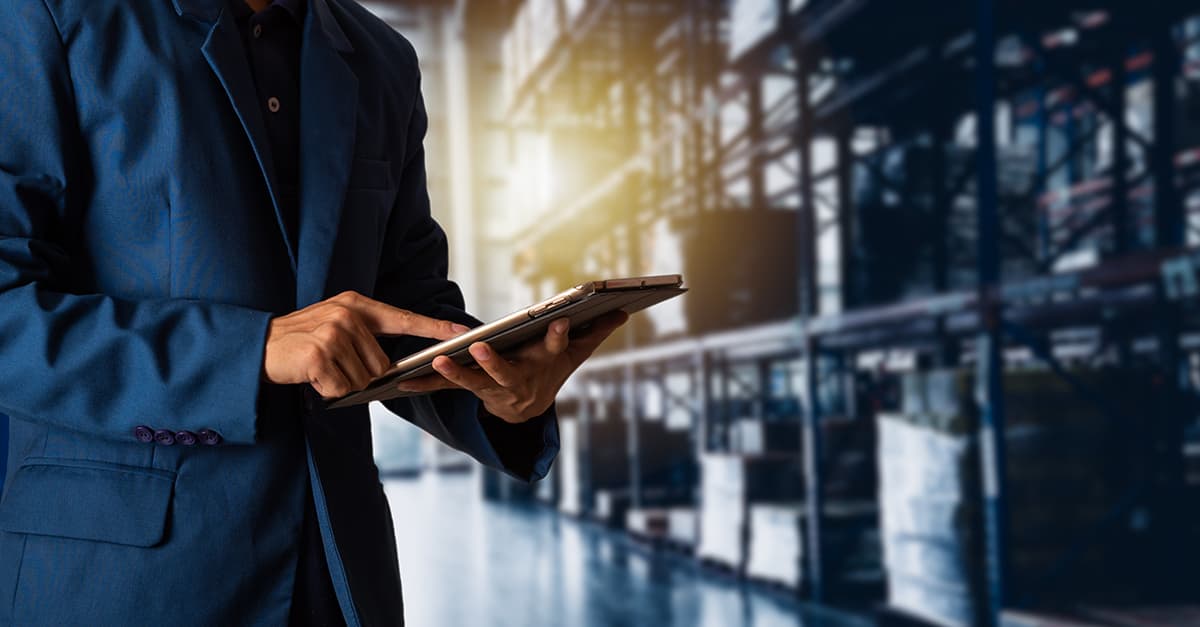
Supply chain fragility is a major concern for c-suite leaders due to an unusual and sustained number of disruptions, such as the pandemic and Russia-Ukraine war. But is it the death knell for globalized supply chains? Globalization was initially driven by cost-cutting, and China’s emergence as “the world’s factory” was fueled by low labor costs, government support and an abundance of raw materials. Yet even before Covid-19, costs in China had been rising. Factor in new political instability, and China’s streamlined ecosystem and economies of scale suddenly look riskier than the flexibility of multisourcing and multishoring. Suddenly, yesterday’s pursuit of efficiency is giving way to the goal of resilience.
“Supply chain resilience and diversification continues to be a key area of focus for economies and companies globally,” says Michael Spiegel, global head of Transaction Banking at Standard Chartered. “This is due to the continued geopolitical, inflationary and protectionism issues that are affecting the reliability of supply chains.”
A forward-looking report by Capgemini Research Institute on supply chains in the consumer-product and retail sectors after Covid found that supply chain disruption is seen as the top risk to business growth for 89% of organizations, ahead of rising raw material prices (79%) and the energy crisis (64%).
The recent past has recast supply chain as a value contributor rather than a cost center. “It needed the pandemic, a vessel blocking the Suez Canal and other major global disruptions” to clarify the impact of supply chains on other business factors, says Jörg Junghanns, head of Supply Chain for Europe at Capgemini. “Revenue growth, cost containment, working capital, customer satisfaction and sustainability—all of these are driven from within the supply chain.”
Diversification strategies include onshoring (within national borders) and near-shoring (to neighboring countries), placing production bases closer to demand, the regionalizing of supplier bases, and widening the manufacturing base to reduce reliance on a single geographic region. “Companies are developing more agile and flexible supply chains and trying to expand their manufacturing and distribution networks,” says Spiegel. “This is costly and hard to execute given the costs and logistics planning involved.”
Aside from the direct economic costs, Patrick Ward, vice president of Marketing at custom-software developer Rootstrap says significant changes in management may also be needed, depending on how complacent companies have become with respect to their suppliers and corresponding expectations.
Multidimensional Matrix
Supply chain resilience is a multidimensional matrix—with lots of elements needing to play along with each other. “You need to understand and know your ecosystem,” Junghanns says. “And you need to build the right partnerships within the ecosystem, which is relevant for a corporation in order to manage, absorb and excel in a supply chain environment.”
Spiegel says clients are increasingly leveraging data and technology for real-time monitoring and detection of vulnerabilities across their supply chains, and for stress testing and contingency planning against possible disruptions. “We’re also seeing an increased focus on responsible sourcing and ESG; this will only grow as supply chains evolve and diversify.”
Capgemini found that 43% of businesses plan to increase investment in resilience, with diversification of supplier bases, production and transportation partners all flagged as priority areas.
“There will be increased diversification of the physical supply chain and of the financial supply chain, particularly as more financial institutions enter the market,” says Frank Tezzi, vice president of Trade and Supply Chain at CGI.
While near-shoring, multisourcing and fostering ecosystems are all very strategic, Junghanns predicts a more tactical need for investments that improve supply chain integration. “I believe continuous investments in the integration and digitalization of the supply chain—primarily into automation, forecasting, prediction and visibility—will help companies master the complexity, and this will make them agile and more resilient.”
“The art behind perfectly balancing offshoring, nearshoring and the sourcing of procurement and distribution requires perfectly planning out your supply chain operations,” Junghanns continues. “If you are sending out your trucks half empty, versus filling them, which requires more thinking and planning and more diligence and sophistication behind what you do, it’s just not very efficient.”
Supply Chains Coming Home
American manufacturing executives are likewise turning toward home, according to Kearney research. The consultancy’s Reshoring Index for 2021 showed 70% of US CEOs were assessing, planning or completing a relocation of operations to regions near the US. Mexico is a popular destination, and 17% had already moved operations there.
Benefiting from tax incentives and streamlined administrative processes, Mexican maquiladoras are attracting new investment for products destined for the North American market. In 2022, US home-appliance maker Whirlpool announced it would invest $120 million to expand production at its manufacturing plant in Ramos Arizpe, Coahuila. Bosch Rexroth, a subsidiary of the German technology group Bosch, announced plans to construct a $215 million facility in Queretaro to manufacture components, reducing the need for transatlantic transport. It is also building skills in-house.
“We are becoming more flexible in handling customer inquiries, expanding our portfolio in the areas of prototype construction, customizing and service,” explains Greg Gumbs, CEO of Bosch Rexroth North America. “[We] will be able to build a more robust regional supply chain.” Bosch has also earmarked $262 million for expanded facilities in both Queretaro and Aguascalientes, and a new facility in Nuevo Leon.
In a move to reduce long-term costs, toy maker Mattel has invested $50 million to expand its Nuevo Leon plant, after closing two factories in Asia and one in Canada. Its proximity to Mattel’s second-largest distribution center, in the Dallas-Fort Worth area, undoubtedly influenced the decision, with Mattel Chairman and CEO Ynon Kreiz announcing that the facility “plays a central role in our reimagined global supply chain operation, providing a strategic footprint for our network in the Americas.”
It isn’t just Mexico benefiting from the nearshoring trend. Lego began construction of a $1 billion new factory in Binh Duong Province, Vietnam, to make products for big markets in the region—including India, Indonesia and the Philippines—that have to date been served by Lego’s factory in China. The China factory will now only serve the domestic market. Lego also has plans to expand its factories in Mexico, which serves North America; and Hungary, which serves Europe.
Lego CEO Niels B. Christiansen says five manufacturing sites on three continents and the new one in Vietnam will make the Danish toy maker’s supply chain “short, flexible, and able to meet shifting demand in our largest markets.”
Manufacturing of apparel has, in the past decade, already shifted to countries like Vietnam, Indonesia, Colombia and Bangladesh, in part due to rising costs in China but also to diversify access to raw materials and production. “Ultimately the theme of the next several decades will be one of contingencies, resiliencies and redundancies as companies learn the lesson of having a single point of failure in their supply chains,” says Rootstrap’s Ward.
Inditex, the owner of clothing retailer Zara, is now able to get new collections into shops within weeks rather than months while reducing its carbon footprint, in part because the company prioritized factories close to Zara’s headquarters in Arteixo, a small town on the northwest coast of Spain. Half of the manufacturers who handle its products are based in Spain, Portugal, Turkey and Morocco. “Having them nearby helps in our efforts to consume less energy and reduce our carbon footprint,” says a spokesperson. “It also allows our team to work closely with our suppliers throughout the whole production process. In conjunction with short runs, proximity offers unparalleled flexibility and control over the process.”
Standard Chartered’s Spiegel notes the “rise of new global trade and logistics hubs, including Dubai, Abu Dhabi and Riyadh in the Middle East and the growth of intraregional trade, for example Intra-Asia and Intra-ASEAN, ASEAN-Middle East,” although he says it hasn’t yet dramatically changed the existing global supply chains of the US, Europe and China, which remain strong.
Ward sees it as unlikely that any one country will dominate trade in the way that China has for the previous two decades. “The perfect conditions of an industrializing nation with a large workforce allowed China to become the global manufacturer—as one of the stylized ‘BRIC’ [Brazil, Russia, India, China] countries. Unfortunately, none of the remaining three are likely to have the same conditions that led to China’s rise, due to population, resources or security constraints,” he says. “Consequently, the global supply chain is likely to fragment into a series of regional supply chains, with companies increasingly focusing on allies for sourcing materials rather than relying on navigating complex relationships with suppliers in potentially hostile nations.”
Flexible Financing
Spiegel highlights the role of banks in supporting companies in identifying and developing new supply chains, thanks to the strength and depth of bank’s on-the-ground market presence and expertise. “Through partnerships, technology and data, banks are now also able to extend liquidity and risk management solutions not only to the large corporates but also to the deep tiers of the supply chain. Standard Chartered is committed to supporting clients in this space. We recently financed the 11th tier in one of our clients’ supply chains through our Deep Tier Supplier Finance solution. These trends are facilitating and accelerating the adoption of digital trade platforms, making trade faster, more transparent, more inclusive and more secure.”
CGI’s Tezzi says the most important technological tool is a robust core supply chain finance (SCF) system that allows the bank to conduct all its SCF business. The system should also be flexible. “SCF is always evolving,” he says. “While more financial institutions [FIs] enter the marketplace, they may take part in participations, risk distribution or the outright sale of specific SCF assets. This will allow FIs to diversify their SCF holdings and risk, and potentially be a part of some larger programs they may not be able to normally access.”
Long lead times, high shipping costs, limited flexibility and the risk of instability are forcing a rethinking of global supply chains. Chris Cox, global head of Trade and Working Capital Solutions at Citi, says resiliency and continuity are taking center stage on sourcing through the production cycle, with “just in case” replacing “just in time” inventory management. “Buyers are now building in more resilience by purchasing earlier and holding more inventory. As a result, financing the end-to-end supply chain remains a top priority. How this trend plays out long term remains to be seen.”