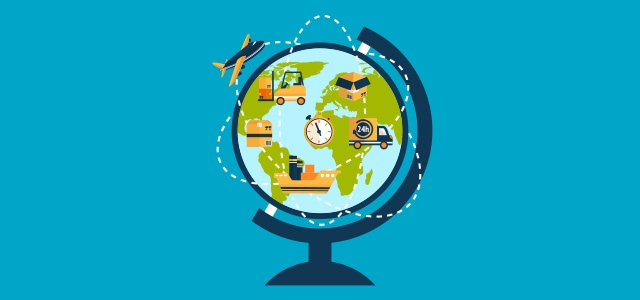
Much has been made of the rush to reshore manufacturing operations by US and European companies over the past couple of years, but very few have brought significant production back home, and those that have, to much fanfare, have also done so in China, India and other markets.
What they are doing is ensuring that they are closer to customers in big markets, which helps to protect them from crippling supply chain disruptions.
Ironically, Toyota, creator of the just-in-time model of production envied and emulated around the globe, has shown the dangers of low inventories and a reliance on too few suppliers from one location. A supply shortage from Japan following the earthquake and tsunami in 2011 forced production halts in Europe and the US, while product recalls in 2010, which resulted in the loss of billions of dollars, were caused by a single part sourced from just one supplier.
Reducing the Risk of Supply Chain Disruptions, a study released earlier this year by Sunil Chopra and ManMohan Sodhi in the MITSloan Management Review, asserts that with supply chains resilience is often sacrificed for cost efficiency, but sees a connection between the two. “Although both require dealing with risks, recurrent risks (such as demand fluctuations that managers must deal with in supply chains) require companies to focus on efficiency in improving the way they match supply and demand, while disruptive risks require companies to build resilience despite additional cost,” the study’s authors write. “Disruptive risks tend to have a domino effect on the supply chain: An impact in one area—for example, a fire in a supply plant—ripples into other areas. Such a risk can’t be addressed by holding additional parts inventory without a substantial loss in cost efficiency. By contrast, recurrent risks such as demand fluctuations or supply delays tend to be independent. They can normally be covered by good supply chain management practices, such as having the right inventory in the right place.”
Chopra and Sodhi recommend two strategies for reducing supply chain fragility through containment while simultaneously improving financial performance: segmenting the supply chain and regionalizing it. They also recommend that companies design business continuity plans because no one is immune to disruption.
This proved to be the case for IBM, which developed and patented its Total Risk Analysis tool a few years ago to meet the complexities of its global supply chain. The computer maker was able to determine all of its potential supplier problems, assemble necessary data and develop backup plans within a few hours of the Japanese earthquake and tsunami.
For most companies, however, this would be impossible. A report by the supply chain experts at UPS Capital, who specialize in risk mitigation, found that 90% of businesses do not formally quantify risk when sourcing production and none of those surveyed use outside expertise in assessing risk for their supply chains.
Interestingly, although the need for increased inventory as supply chains go global was the second greatest risk identified, nearshoring was not seen as a risk mitigation solution. So although companies understand that having a global supply chain—rather than just domestic—requires that they carry at least 60 to 75 days of additional inventory, this doesn’t mean they are rushing back home.
Most companies realize that trying to put out supply chain “fires” after they start burning is not an acceptable approach to supply chain risk management, but the majority still don’t follow the three-step risk management process of identifying, prioritizing and mitigating risk.