3D printing continues to displace traditional manufacturing methods.
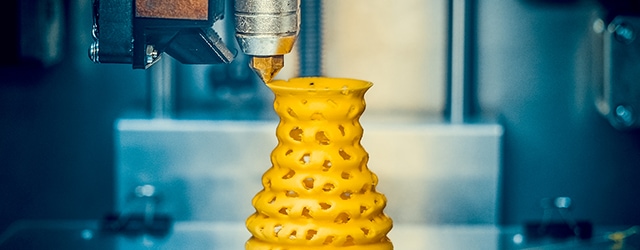
Computer 3D printing (3DP) is being widely adopted in high-volume industrial sectors such as aerospace, automotive, healthcare and defense. Universities and other educational institutions also have incorporated 3DP into their technical training programs.
“3DP addresses the issues of cost, weight and reliability,” says Debbie Naguy, chief of the Product Support Engineering Division at the US Air Force Life Cycle Management Center in Dayton, Ohio. “It is prevalent everywhere, from aviation to automotive.”
3D printing is also called additive manufacturing (AM). Traditional manufacturing starts with a slab of material and eliminates whatever is unnecessary to form an object, creating waste that carries financial and environmental consequences. Additive manufacturing, by contrast, layers powdered alloys to build a three-dimensional object. The improved accuracy, enhanced product design and shorter time to market demonstrably lower costs. Leftover material can be reused. AM requires design to be done on computers, so it can be uploaded to the 3D printers.
“There has been a profound shift away from drawing on paper,” says Bradley Rothenberg, CEO of nTopology, which designs software for AM.
According to the Wohlers Report 2019, from consulting firm Wohlers Associates, the US is home to more than one-third of all industrial AM systems, followed by China with 10.6% and Germany with 8.3%. San Francisco-based Grand View Research expects 3D printing to deliver a compound annual growth rate of 16.5% and reach $23.79 billion by 2025. Naguy says the US Air Force plans a global network of qualified printers.
“We’re marketing in the direction of all industries,” says Mark Shaw, additive leader at GE Additive. But, he cautions, “We have to reimagine the supply chain. … There’s still the burden for assuring quality.”
3DP is capital-intensive, lacking in standard process controls and a trained workforce. These factors may initially hinder growth. Still, as Naguy says, “the art of the possible is huge.”